|
Graham Packaging is the world's largest processor of high density polyethylene (HDPE) products. When Graham acquired their Port Allen, La. facility from another company several years ago, production capacity for onequart bottles they manufacture to carry Castrol motor oil was limited by the existing out-dated equipment. Graham quickly replaced the original blow-molders with machines that they designed and built internally. These state-of-the- art molders theoretically tripled the plant's capacity. Achieving that higher production rate in practice, however, depends partly on rapidly cooling the plastic below its softening point by using low-temperature water-glycol mixture for cooling the bottle molds.
These cold mold surfaces can create problems during the humid weather Louisiana is famous for. When chilled molds open to release the bottles, water condenses out of the humid air onto the cold surface. This condensation, often called "mold sweat", causes several problems:
- Bottle surface looks like "orange peel" because water droplets form bumps on the mold surface;
- Condensation accelerates corrosion, which increases maintenance costs;
- Most importantly, surface deformities forming around the water droplets prevent the proper adhesion of labels.
Graham's problems are not unique. They are, in fact, common wherever plastic-product manufacturers use cooled molding equipment.
In many plants, production managers opt to reduce mold sweat by holding their chilled-water temperature above the ambient dew point. Doing so, however, reduces the speed at which the thermoplastic hardens, ultimately slowing down production.
Rather than accept such a low production rate, Graham decided to bring in desiccant dehumidifiers manufactured by Munters Corporation in Amesbury, Mass. to dry out the air surrounding the molds. These units reduce the dew point of the air surrounding the molds, eliminating condensation and allowing continuous, high-speed operation.
Molding Process
Rather than accept such a low production rate, Graham decided to bring in desiccant dehumidifiers manufactured by Munters Corporation in Amesbury, Mass. to dry out the air surrounding the molds. These units reduce the dew point of the air surrounding the molds, eliminating condensation and allowing continuous, high-speed operation.
The blow molding process begins with a "pre-mold," which is an open tube of thermoplastic extruded through a die. The material comes from a pressurized hopper heated to several hundred Fahrenheit-above the material's plastic temperature.
As the hot material leaves the die, two metal mold halves, shown in Fig. 1, clamp around it. Compressed air blown into the pre-mold tube's interior forces the material against the mold's interior surface. The plastic gives up heat to the cooler mold surface until it cools to below its plastic temperature and hardens.
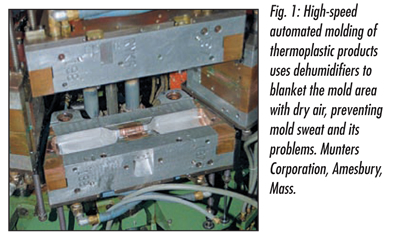
|
 |
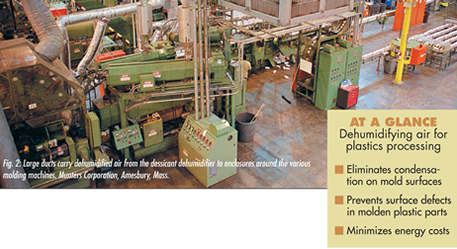
Actively cooling the mold keeps heat from building up in the metal. It can also increase the production rate by reducing the mold temperature below ambient. The cooler the mold surface, the faster the plastic gives up its heat, the sooner it reaches its plastic temperature and the greater the molding machine's throughput.
Water droplets condensing on the mold's cold surface while it is open form pits and other features on the surface. The water, of course, flashes into steam as soon as the hot pre-mold hits it, but that steam becomes trapped between the pre-mold and mold. Pressure of the trapped steam holds the pre-mold away from the mold while the plastic cools, forming the unwanted ripples and pits that ruin the surface finishTo prevent condensation, Graham installed enclosures around the molds to limit air intrusion, and piped desiccated air into the enclosures as shown in Fig. 2. The desiccated air starts out as ambient air pulled into a desiccant dehumidifier. One dehumidifier can serve several automated molding machines.
There are a number of ways engineers can reduce air's humidity. The least expensive and most reliable way of producing dry air in high volume is with a desiccant dehumidifier.
The system's heart is a desiccant wheel shown in Fig. 3. As process air flows through the wheel, the desiccant pulls water vapor from the air and traps it.
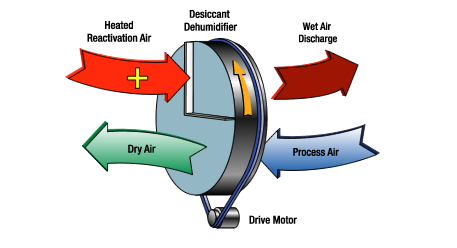
Fig. 3: Desiccant dehumidifiers work by transferring moisture from the process air to reactivation air across a desiccant wheel. Climate by Design International, Owatonna, MN.
"The wheel is approximately 15 inches deep," says Jeff Siemasko, Manager of Marketing and Business Development at Munters, "rotating at six to ten revolutions per hour. The wheel acts like a sponge that works on a vapor pressure differential between the desiccant and the airstream. Water vapor is adsorbed into the pores of the desiccant. The wheel is made of ceramic fiberglass paper and resembles wound corrugated cardboard. This geometry allows for a large desiccant contact area with a reasonable pressure drop."
Click here for page two of Energy Choices for Plastic Processing |
|