Interior mold prevention consideration needs to be taken into account when designing a building. The vapor barrier needs to be placed closest to the warm surface to reduce the potential for interior wall condensation. See figure 3. This can be challenging in an ice arena as some building contractors have placed the vapor barrier on the wrong side of the insulation systems allowing water vapor to penetrate through the porous insulation and condense on the "cool side" exposed to the interior of the ice arena. The ice arena provides a cool surface in the summer months when the outdoor humidity levels are the highest.
As high humidity air penetrates the exterior siding, it moves through the porous insulation until it reaches the dew point. Then it will condense as liquid water. This interior wall high humidity condition can promote mold growth. The interior surfaces of an Ice Arena are always cool relative to summer ambient conditions. The integrity of the vapor barrier is important to retard internal wall mold growth.
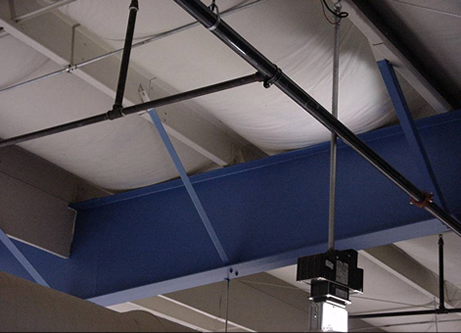
Figure 4: Bat insulation with vapor barrier in the inside (COLD) location allowing the accumulation of water.
The major controllable area in ice arenas is the infiltration of outside air and conditioning of outdoor air. In the summer months outside air brings large quantities of moisture into the cool ice arena. Each 1,000 SCFM of outside air can bring in up to 6 gallons of water vapor. Typical building codes require small recreational arenas, with less than 200 seats, to bring in up to 11,000 SCFM from the outside to maintain good control of CO2. If this air is brought in unconditioned, the rink can condense 66 gallons per hour on the ice sheet and interior components.
|
Design recommendations for desiccant dehumidification systems target 35 degree dew point with 55 degree rink conditions. This will provide an interior relative humidity of approximately 40% which will retard any potential mold formation on most surfaces in the arena. Any interior surface will have to be less than 35°F to condense moisture. It is important to monitor and maintain proper interior relative humidity to eliminate the potential for mold and promote a healthy environment. In the event of pipe break or flooding it is important to dry the building quickly so mold can establish itself. Additional rental dehumidifiers may be required to quickly dry out the structure. Many water damage contractors have the proper tools to quickly dry out a building so replacement of walls and flooring is not required.
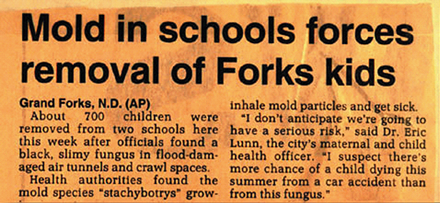
If a manager suspects mold contamination, what should he/she do? The first issue is to determine the cause and correct it. The legal community has targeted mold as a potential health threat. Because children may be involved, it is important to react properly and quickly to correct the situation. Remediation contractors and microbiologists recommend complete replacement of contaminated building products once mold is present. If the existing mold cannot be killed, it can be bleached to stop the growth, but once the area becomes moist again the mold will continue to grow. With some molds, quickly drying the space will cause the molds to release more spores in search of a new home. Tests can be performed by microbiologists to determine the type of mold and recommend remediation steps.
Most experts agree that the key to mold control is moisture control. If remediation is required the Environmental Protection Agency (EPA) has a "Mold Remediation- Keys Steps and Resource List" available on the EPA website. Most large communities have water damage remediation contractors available to advise on mold problems. It is important that the contractor selected is trained in mold abatement procedures to insure proper containment and disposal of damaged building materials. The best prevention is to control humidity however, if mold is present in an ice arena facility, seek immediate help from qualified professionals.
Resource Information
The U.S. Environmental Protection Agency www.epa.gov/indoor-air-quality-iaq
The National Indoor Air Quality Association www.iaqa.org/
References:
ASHRAE Humidity Control Design Guide
ASHRAE IAQ Applications Newsletter Fall 2002 "The Proposed Mold law"
US Environmental Protection Agency "Mold Remediation in Schools and Buildings"
National Indoor Air Quality Institute. "Indoor air Quality Solutions",
"Asthma and Indoor Air Quality"
Engineering and Fire Inspections "Got Mold"
|